In modern manufacturing and logistics, ensuring the quality of products during every stage of the supply chain is critical for customer satisfaction and operational efficiency. Quality control is a strategic approach that prevents defective goods from reaching the end user and helps companies maintain a consistent standard across production and transfer operations. In Odoo 18, the Quality module is tightly integrated with inventory management and transfer processes, making it easier to implement structured and efficient quality assurance measures across the supply chain.
The Quality module in Odoo 18 allows businesses to monitor the condition and conformity of products during key stages, such as when goods are picked, received into inventory, or shipped to customers. By configuring quality control points, companies can automate inspections at specific phases of a transfer operation. These control points act as checkpoints that prompt the system to initiate quality checks at predefined stages, helping businesses quickly identify and rectify any defects or inconsistencies.
To begin setting up quality control for transfer operations, users can navigate to the Quality Control Points section within the Quality module.
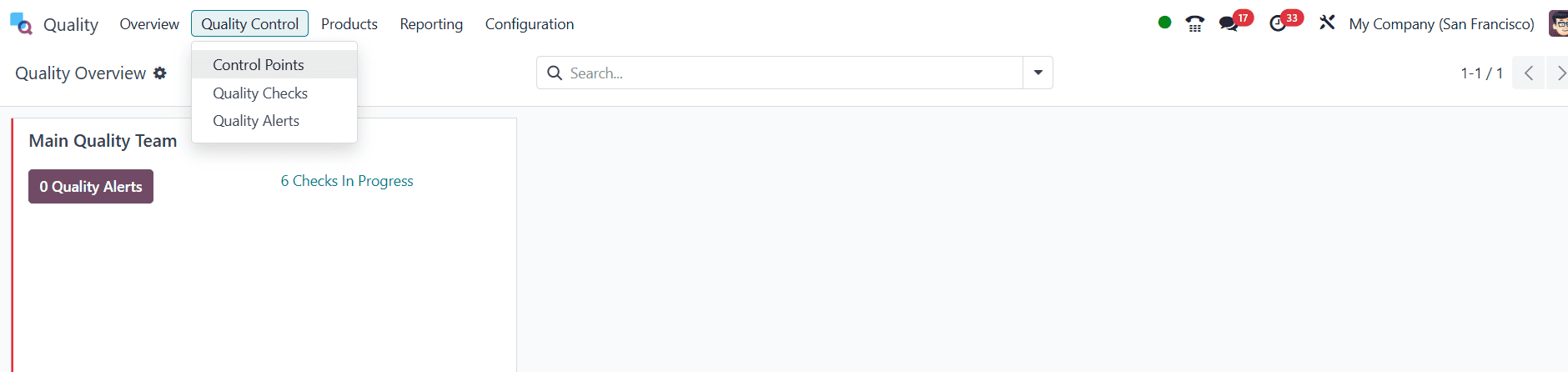
Creating a new control point involves filling in critical details such as the Title (a recognizable label for production floor teams), Product or Product Category (indicating which items are subject to inspection), and the Operation Type (such as Delivery Orders, Receipts, or Returns).
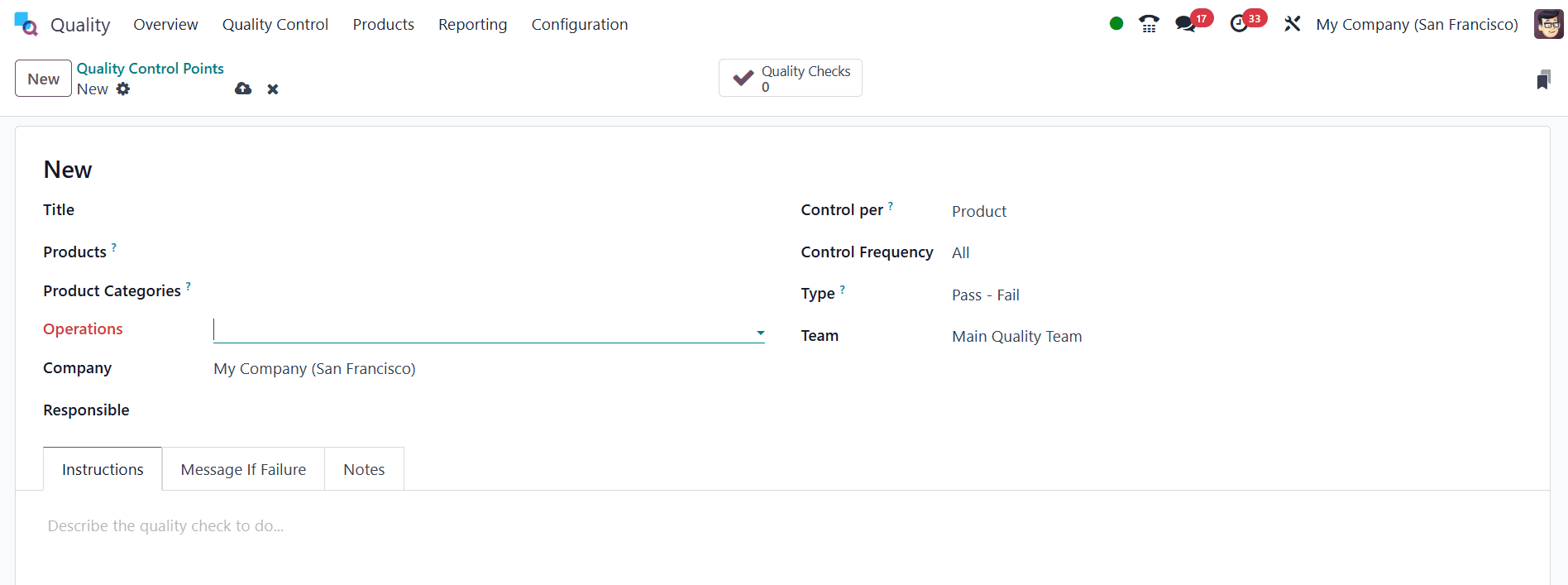
This configuration ensures that only the relevant operations trigger quality checks. Additionally, the control point form allows you to define the Company applying the control point, assign a Quality Team, and specify the Control Frequency, options include "All Operations", "Randomly", or "Periodically" based on your quality policy. The Type of control, whether it's a simple instruction, a pass/fail check, or even a photo requirement, helps standardize the inspection method.
Further customization is available through the tabs at the bottom of the form. The Instructions tab provides detailed steps for performing the quality check, while the If Failure tab offers predefined actions in case a product fails the inspection. A general Notes section is also available for any additional information that inspectors may require.
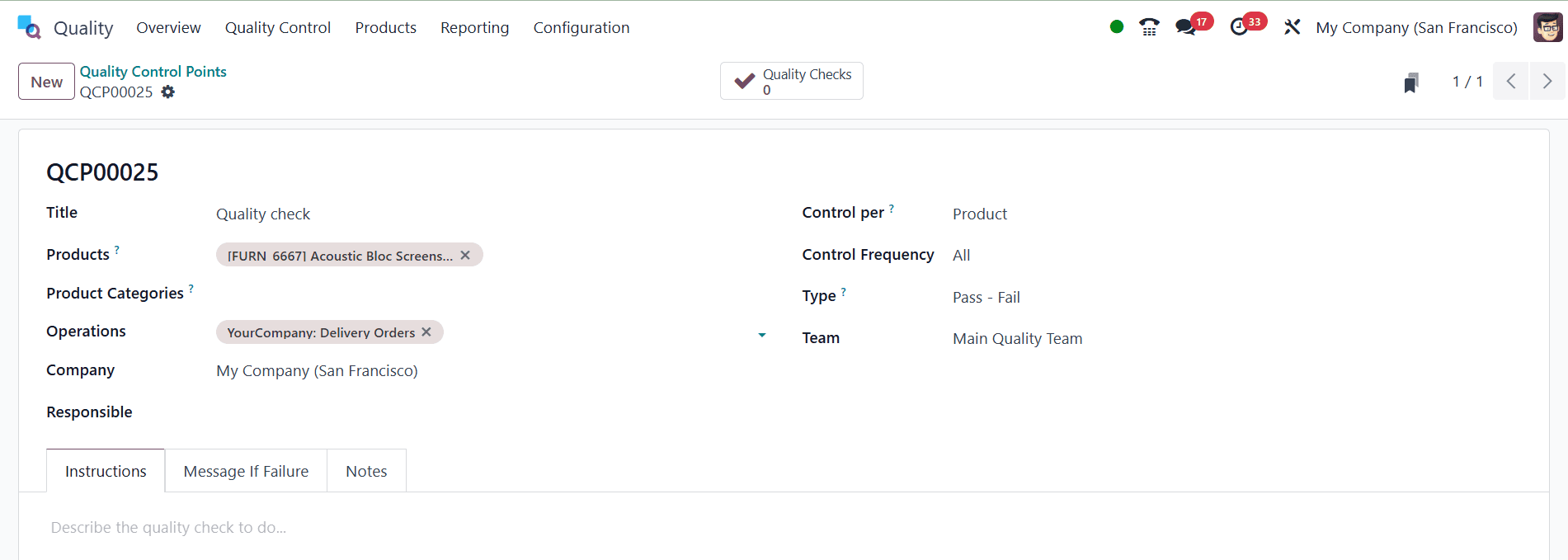
Once a quality control point is created, Odoo automatically generates a Quality Check record when a matching operation, such as a delivery or return, is processed. In this example, we are setting up quality checks specifically for the product “Acoustic Bloc Screens” under the operation type Delivery Orders.
Now, let's create a Sales Order for the product “Acoustic Bloc Screens” and walk through the quality control procedure in Odoo 18. Begin by navigating to the Sales module and creating a new Sales Order by selecting the customer and adding “Acoustic Bloc Screens” as the product.
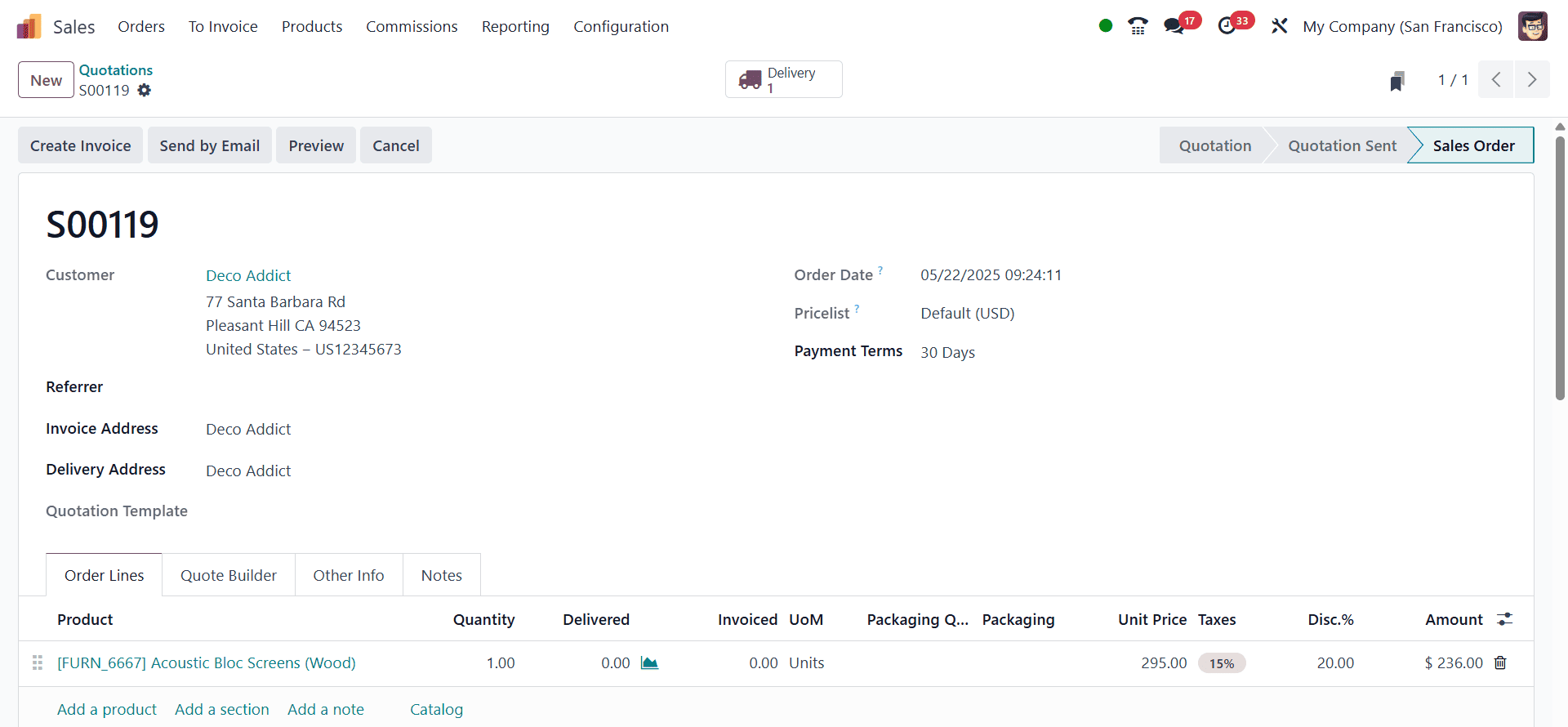
Once the order details are filled in, confirm the Sales Order. Upon confirmation, a corresponding Delivery Order will be generated.
Now, go to the Inventory module and open the delivery order linked to the Sales Order you just confirmed.
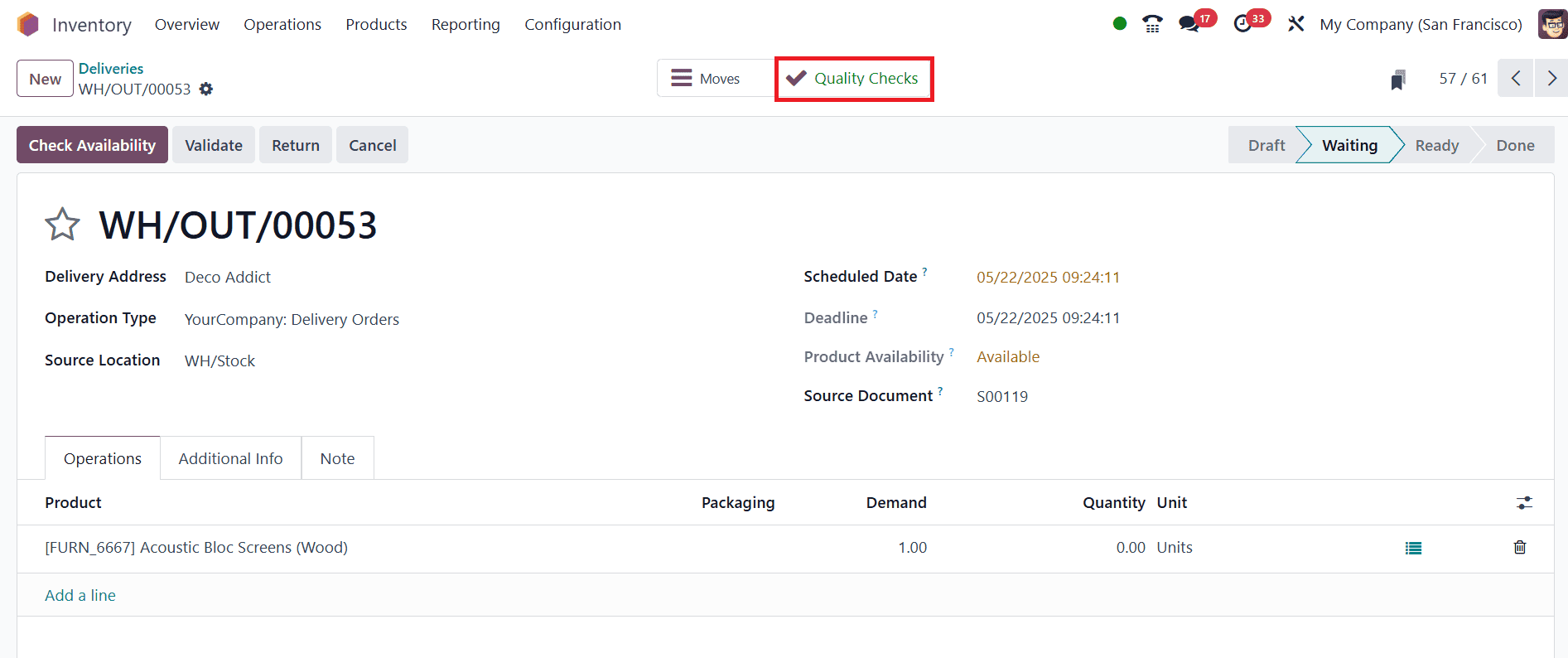
On the delivery order form, you will notice a Quality Check button, provided that a quality control point has already been configured for this product under the operation type Delivery Orders. Click on this button to initiate the inspection.

The list of quality checks will be displayed here.
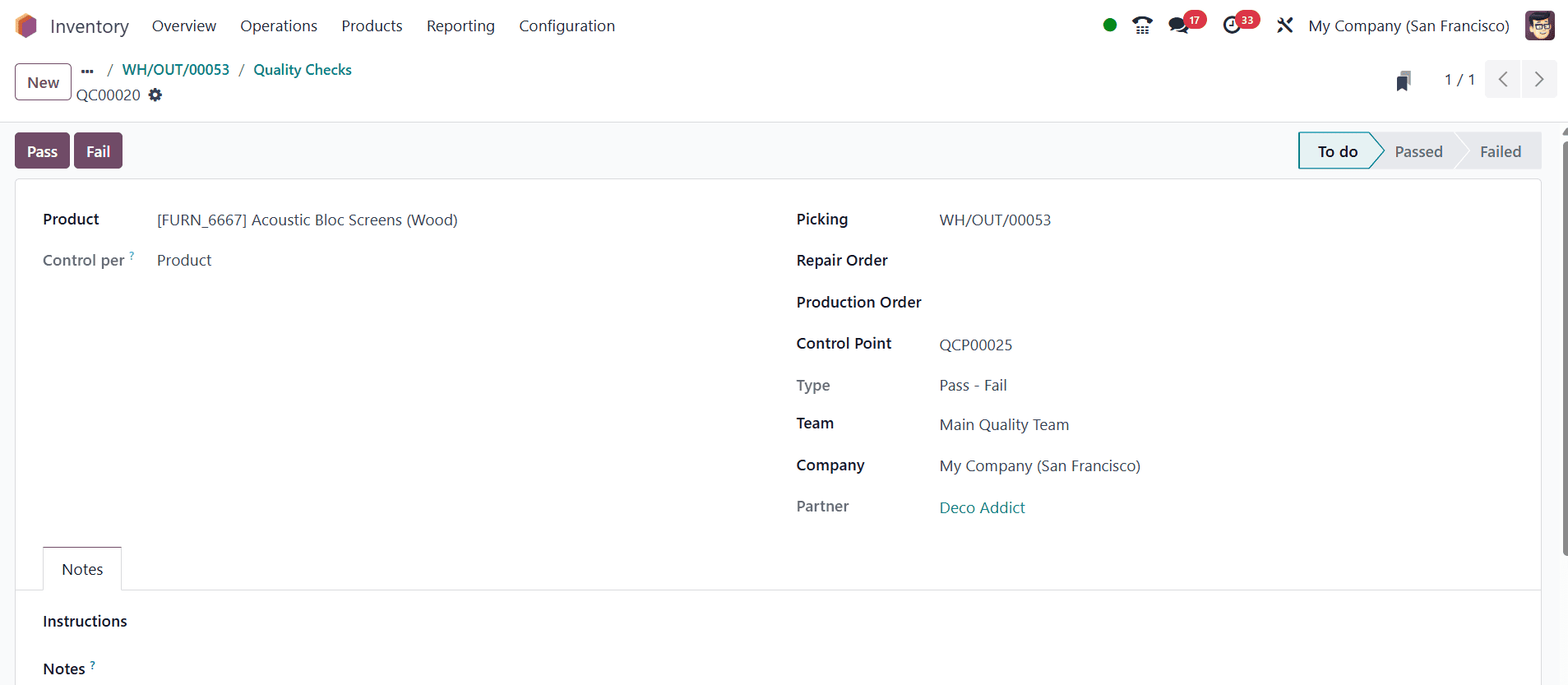
A window will appear, allowing the assigned quality inspector to evaluate the product. The inspector can then mark the inspection result as Passed or Failed, depending on the outcome, and also record any specific comments or observations in the provided field.

Once the quality check is completed and marked as Passed, Odoo visually confirms the success of the inspection by displaying a green checkmark on the Quality Checks smart button on the delivery form. This ensures that “Acoustic Bloc Screens” has undergone proper quality verification before being dispatched to the customer, maintaining high standards of product quality.
Let’s now examine how the quality control process in Odoo 18 functions during a Return Transfer using the same product, “Acoustic Bloc Screens”, as our example. Once the initial Sales Order for the product has been confirmed, delivered, and the quality check has been completed as described earlier, a customer may request to return the product for any reason, such as damage, defects, or dissatisfaction.
To initiate the return, go to the Inventory module and open the original delivery order related to the “Acoustic Bloc Screens.” At the top of the delivery order form, click the Return button.
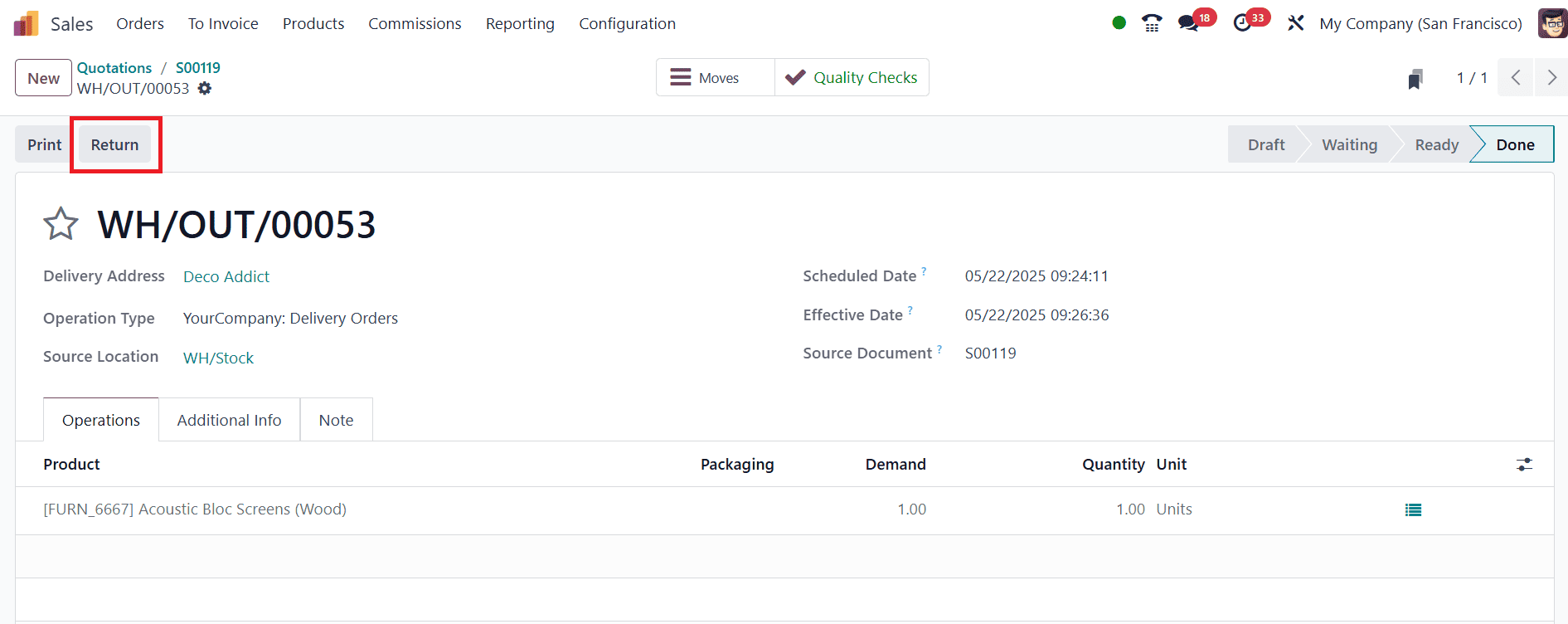
This generates a reverse transfer that records the movement of the product back into your warehouse. Upon confirming this return transfer, Odoo automatically activates the Quality Check button for this operation, provided a quality control point for Returns has been configured for the product.
Clicking the Quality Check button opens a window where the quality inspector can assess the returned item. This inspection step is crucial as it allows the warehouse or quality team to examine the returned goods and determine whether they are in a sellable condition or need to be repaired, scrapped, or quarantined.
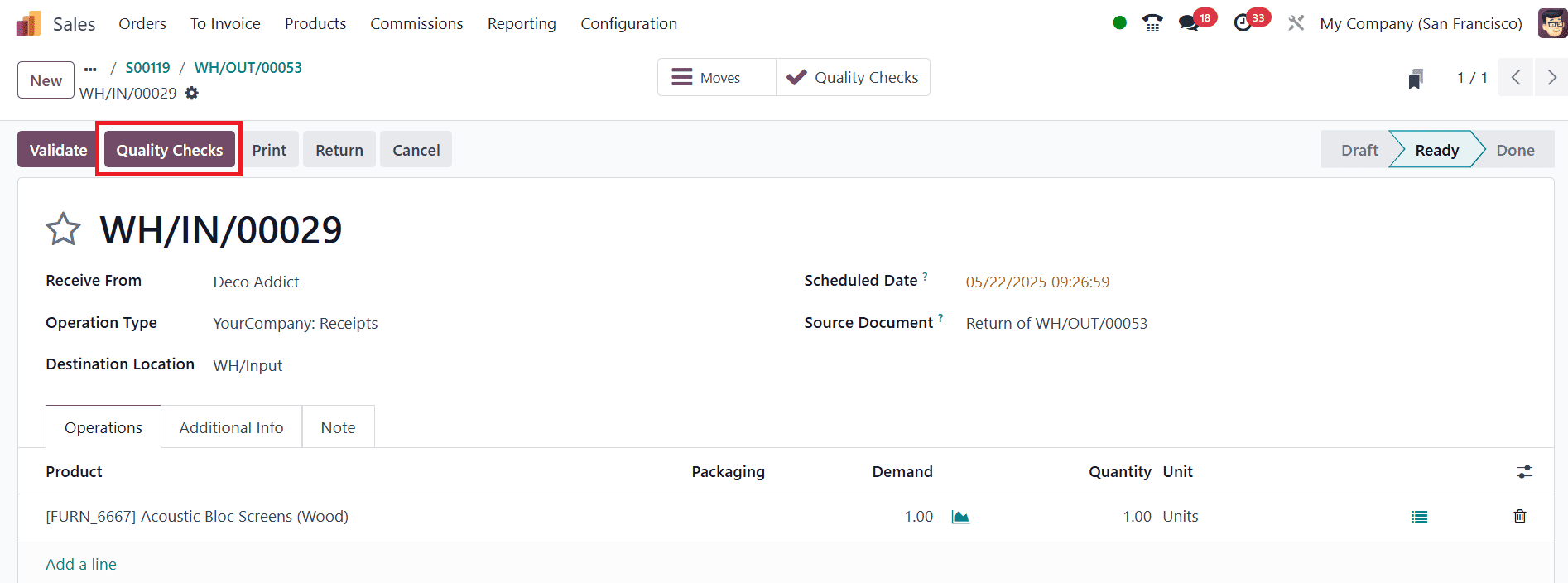
The inspector can enter comments, mark the result as Passed or Failed, and finalize the check.
Once the inspection is completed and marked as Passed, Odoo updates the Quality Checks smart button with a green checkmark, just as it does during the delivery process.
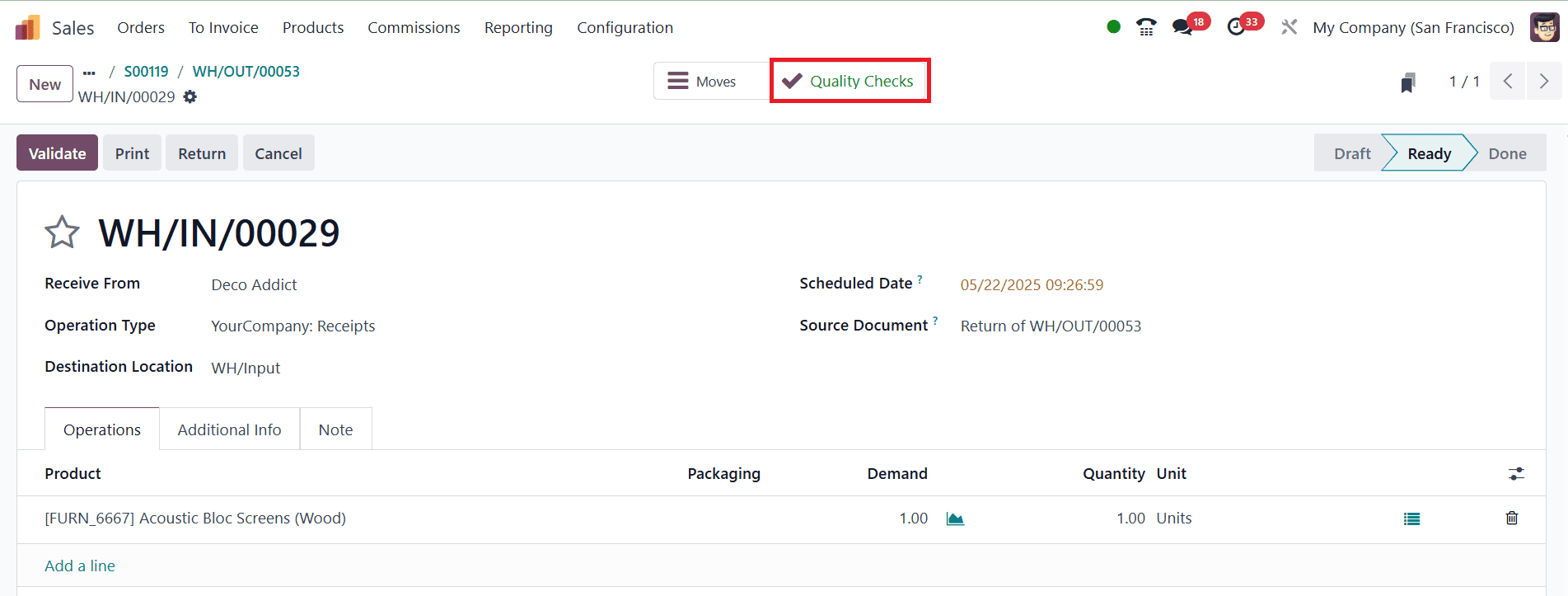
This visual confirmation indicates that the return has been evaluated and approved for re-entry into inventory. If the return fails the quality check, the product can be flagged accordingly and routed to a separate location or process for defective items.
By implementing quality control during both outbound and inbound transfer operations, Odoo 18 empowers organizations to maintain high standards and reduce errors. The integration of the Quality module with Inventory operations offers a proactive framework that not only safeguards product integrity but also enhances transparency and accountability across teams. Ultimately, this contributes to better decision-making, improved customer satisfaction, and a stronger brand reputation.
To read more about How to Set Up Quality Control for Transfer Operations in Odoo 17 Inventory, refer to our blog How to Set Up Quality Control for Transfer Operations in Odoo 17 Inventory.